Stamping Press Machines Components
Quick Die Change System in Press Machining
The Pascal Quick Die Change System (QDC) utilizes automated die clamps to increase productivity by reducing the downtime associated with traditional die change methods.
Die clamping is simplified by integrating hydraulic or pneumatic die clamps, and loading the die is made significantly easier with a die changer. Time savings and safety are ensured by using our press machine components, which increases satisfaction on the part of operators, production managers and customers alike.
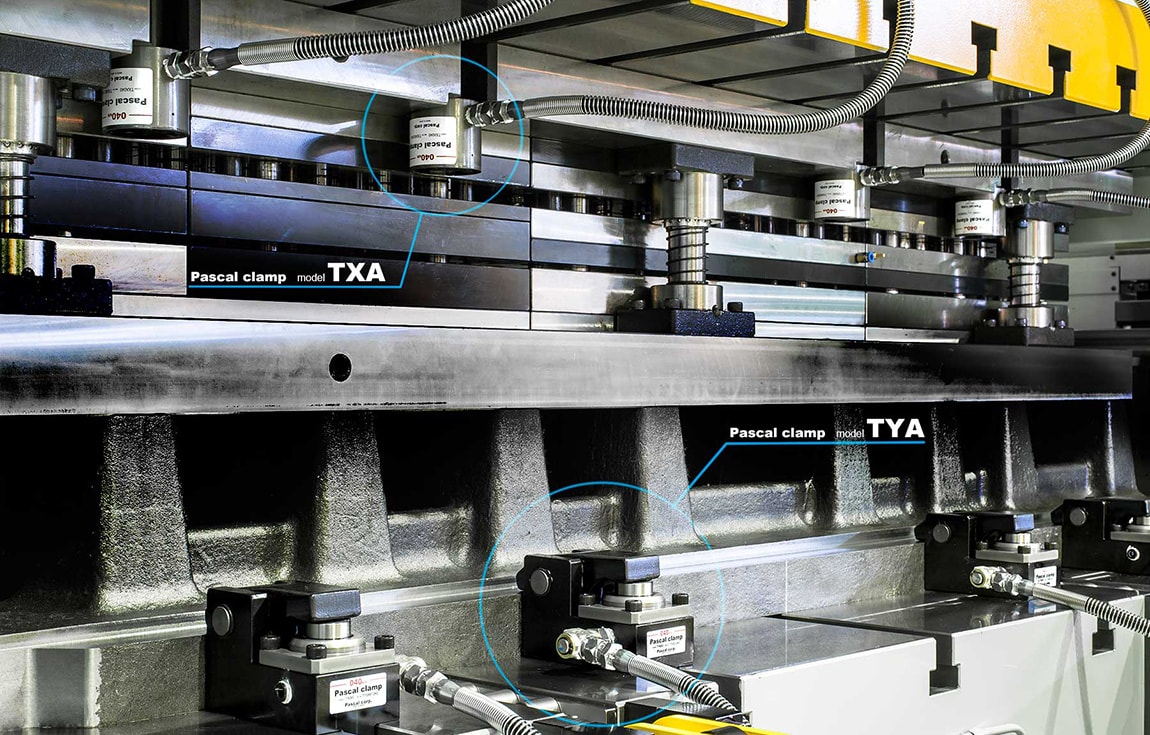
Benefits of Using Automated Die Clamps
Improved Safety
Someone forgot to place or remove a clamp, and as a result the die dropped. Sound familiar? A simple mistake could be extremely dangerous for the operators, because the mold could fall on them.
Manually checking each clamp, could lead to user error. Pascal’s hydraulic or pneumatic clamps are available with a sensors, allowing you to verify where the clamps are at all times. Clamps with sensors, along with a Pascal operation and control panel provide a safety interlock system will not let the die change continue until all clamps are in the proper position.
Using a forklift to load the die could risk someone getting injured in a pinch point, and the die could sustain damage. A die changer will load the die into the stamping press machine without the use of a forklift.
Pascal offers a number of safe hydraulic press components to suit your specific needs, including die changers, die carts, die lifters and pre-rollers.
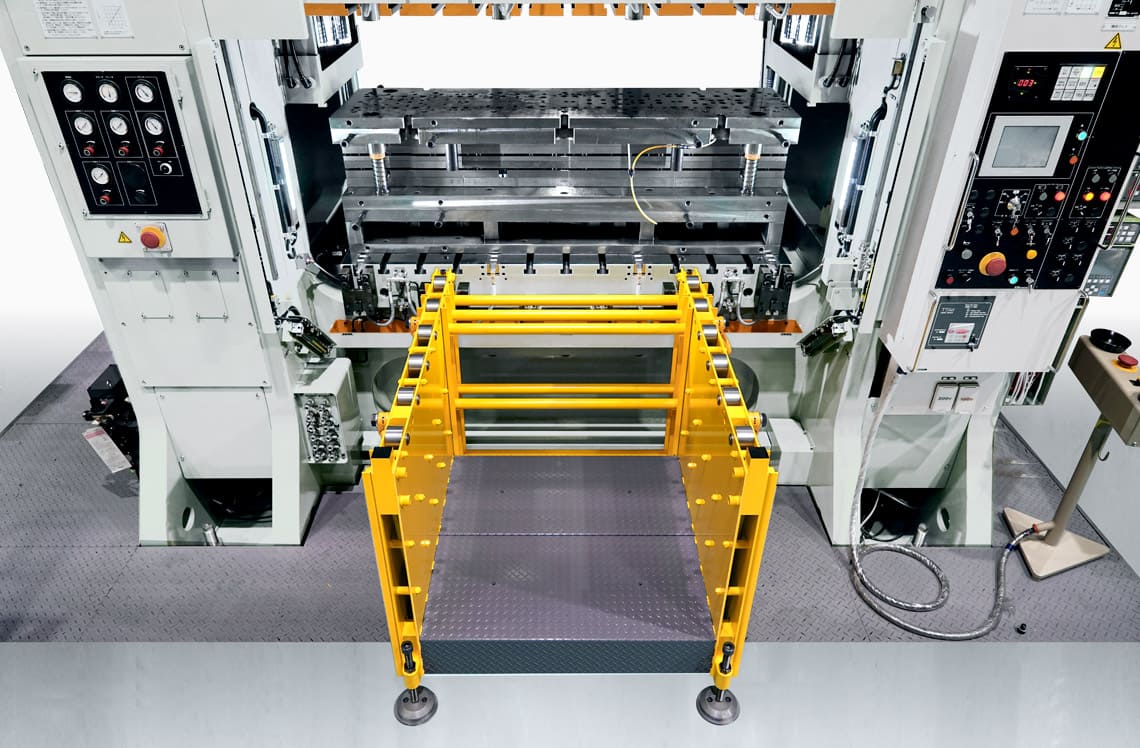
Greater Productivity
Placing the die in position in the metal stamping press, securing the die clamps, and performing a die change manually can take a lot of time. Time wasted on die change can affect delivery. The time spent on a die change is time taken away from production — and this can result in missing a delivery schedule.
Use of Pascal’s Quick Die Change (QDC) system can potentially gain many hours for production, drastically reducing downtime.
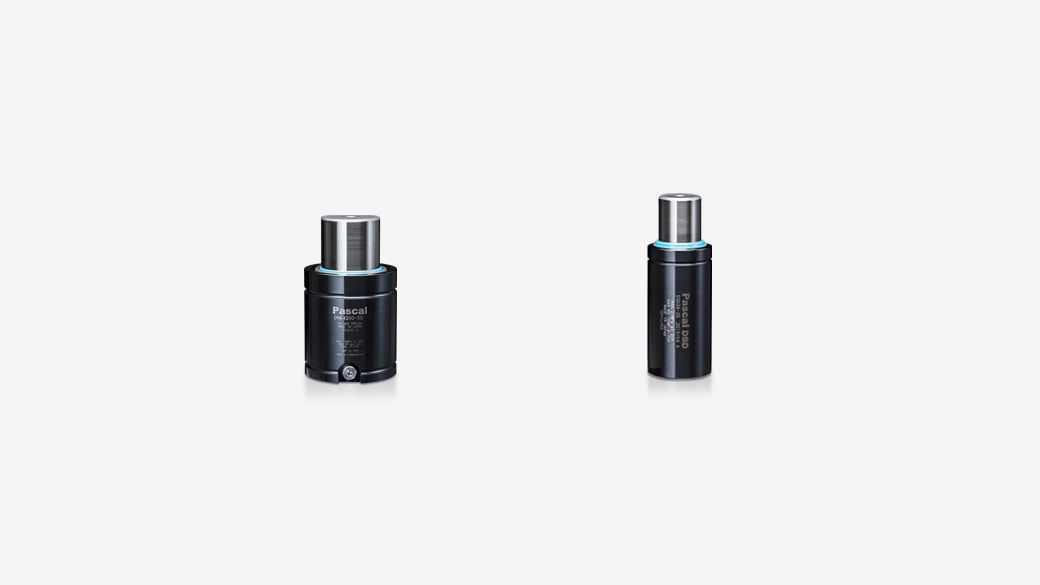
Gas Springs in the Stamping Business
In the stamping business, downtime resulting from frequent coil spring failure can be costly. Gas springs are good alternative press machine parts for reducing downtime and improving product quality. A die with coil springs can be retrofitted with Pascal gas springs with simple modifications to meet your needs. We stock gas springs in our warehouse to provide same-day shipping for these critical press machine components.
Gas Springs in Press Machining
Gas springs have become popular in stamping die applications in recent years because gas springs have many advantages over conventional coil springs. Advantages of the gas spring include higher initial contact force, availability in compact profile (smaller shut height) and durability. Since these hydraulic press parts are compact and capable of producing high force, fewer springs are required to achieve the desired force, which means that the die can be built with less machining and less material, resulting in reduced weight.
Gas Spring Application in Automotive
Pascal gas springs are available in many strokes and sizes to meet the required force within the die. Typical applications for these hydraulic press components are lifting stock, drawing (to hold the bead), blanking (to strip the punch) and piercing (stripper plate, stripper unit and cam units).
The increased use of High Tensile Strength Steel (HTSS) in recent years has resulted in a growing need for the gas springs. HTSS is very strong yet lightweight, and the reduced weight improves the vehicle’s fuel efficiency without compromising safety. Also, because HTSS is brittle and difficult to form compared to conventional steel, more initial force is required than coil springs can achieve.